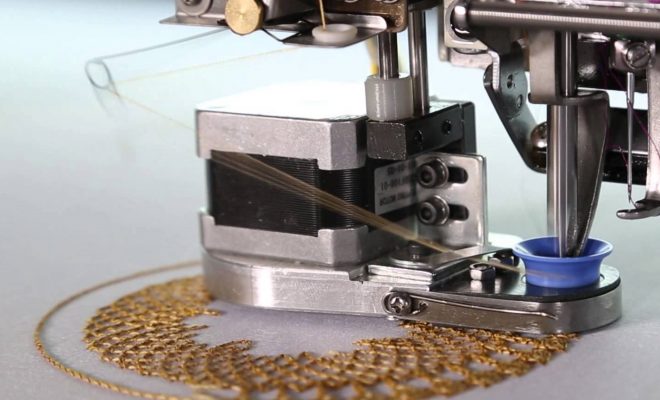
Embroidery
Complete Guide to Buying Your Very First Embroidery Machine
There are three starting questions you need to know the answers to before you decide on which machine to buy:
1) Is this for hobby or business use?
2) What size embroidery field do you want to sew?
3) How much are you willing (or able) to spend?
The first question is “business or hobby?” If it is for hobby use, there are lots of options, starting around $500 and going up – way up! For a business, you will need a machine that can sew a lot of stitches pretty quickly. A home machine does not need to be as fast or heavy-duty as a business machine.
The second question is about “field size.” The more expensive machines will sew designs larger than 4″ x 4″ without needing to re-hoop your design to continue. While rehooping is an option, it is another step and another opportunity for error. Almost all the designs we make fit in a 4″x4″ hoop, but there are plenty of designs that won’t on the market. Home machines can go up to 10″ x16″ sewing area. Commercial machines can do the back of a jacket with one hooping. If you will be happy with a 4″x4″ hoop, you can save quite a bit of money on the machine cost.
The third question is “how much are you willing or able to spend?”
I will start with this cost question first, since it is usually formost in people’s minds. There are several home machines around $500 and the top end home machines sell for about $7,000 list price. Commercial machines start around $7,000 and go up to $20,000 for a “single-head” machine. A single head machine embroiders one garment at a time. A two-head machine will be more like $30,000 to $40,000, and so on. A commercial machine is necesary for mass production sewing. So… for home use, budget from $1,000 to $7,000. For a business, budget $7,000 to $20,000 or more.
Along with the machine, you will need a way to get designs from your computer into the embroidery machine. Depending on the machine you buy, there are three common ways to do this. The most common method is through a memory card. You can buy pre-programmed cards at your dealer at an average price of $60 each. Some cards can cost over $100 and sometimes you can catch a closeout sale at $20 each. These cards usually have 10 or 20 designs on each one. You just buy the card, insert it into a slot on your machine and then pick which design you want to sew out.
If you buy a machine that only accepts memory cards (almost all machines under $4,000 take memory cards only) then the number one accessory you should consider is a card-writer. It is a small box that plugs into your pc and allows you to write designs from your computer to a blank memory card. After you sew that design out you can erase it and write another design to the card. It’s reuseable. The most popular card-writers are the “magic box” and the “Ultimate Box”. Either will cost about $200 and is well worth the investment. A card-writer box will quickly pay for itself by saving you money on pre-programmed cards.
The second most popular way to get designs into your machine will be through a USB or Serial cable from your pc directly to the sewing machine. Several home machines in the $4000 and up price range have this option. Note that your pc must be close to your sewing machine to use this method.
The final way to get designs into your embroidery machine is through a floppy disk. Some higher priced home machines have a standard floppy disk slot on them and you simply save a design from your pc to a floppy disk and then stick it into the machine.
You also may want to buy software for managing or manipulating designs or for making your own designs.
Most software for “manipulating” (editing) designs will be more expensive. Embird can do some editing and is a good choice at a very reasonable price. Other programs from your machine manufacturer will probably cost $400 to $900 to do these tasks. You can resize designs (up or down 10%) sometimes with this software, save designs that were made for a different brand of machine in your machines required format. Remove parts of a design or add parts or lettering to a design as well as combine two designs into one with editing software.
Software for creating your own designs is called “digitizing” software. The starting price for digitizing software is about $1,000 and it goes up quickly to $1,500 to $5,000 or more. Please note that digitizing software is NOT intuitive. There is a learning curve and it requires time and practice to make designs. No matter how simple a salesperson makes it look, it will take a lot of effort to get good with it. We joke about the first design Holly made taking her six months and two hours. She spent two hours making her first “real design” after spending six months of diligent learning time.
0 comments